Zirconiated Tungsten Electrodes Advantages
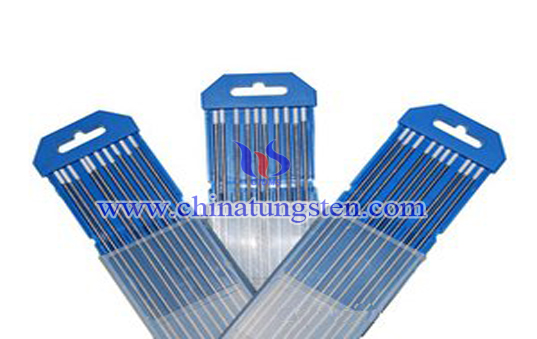
Zirconiated tungsten electrodes have a better weldability than some more common construction materials, provided that the proper procedure is followed. Proper shielding from air with inert gasses such as argon or helium is very important when welding these metals. Because of the reactivity of zirconium and hafnium to most gases at welding temperatures, welding without proper shielding will allow the absorption of oxygen, hydrogen, and nitrogen from the atmosphere and thus embrittle the weld. Zirconiated and hafnium are most commonly welded by the gas tungsten arc welding (GTAW) technique. Other welding methods used for these materials include gas metal arc welding (GMAW), plasma arc welding, electron beam welding, and resistance welding.
Zirconiated tungsten electrodes have low coefficients of thermal expansion and thus experience little distortion during welding. Inclusions are not usually a problem in the welds because these metals have a high solubility for their own oxides, and because no fluxes are used in welding, flux entrapment is eliminated. Zirconiated and hafnium both have a low modulus of elasticity; therefore, residual stresses are low in a finished weld. However, stress relief of these welds has been found to be beneficial. A stress-relief temperature of 550 oC (1020 oF) should be used for both zirconium and hafnium.
Zirconiated tungsten electrodes are subject to severe embrittlement by relatively minute amounts of impurities, especially nitrogen, oxygen, carbon, and hydrogen. They have a high affinity for these elements at the welding temperature. Because of this high affinity for gaseous elements, zirconium and hafnium must either be welded using arc welding processes with inert shielding gases, such as argon or helium, or be welded in a vacuum. Hafnium ductility is affected to a greater degree by oxygen absorption than is zirconium ductility.
Arc welding in an inert blanket using either a tungsten electrode or consumable electrodes of zirconium gives the best results. The weld puddle, and the backside of the weld must all be protected from the atmosphere in some manner. The weld puddle and the bead just behind the weld puddle can be protected by secondary shielding, such as a trailing shield.
The most common techniques used for zirconium tungsten electrodes are the inert gas GTAW and GMAW methods. This equipment can be set up and used in the manual or automatic welding modes. Alternating current or direct current can be used for gas tungsten arc welding. Straight polarity is preferred for welding with a consumable electrode filler wire because this results in a more stable arc.