Zirconiated Tungsten Electrodes Applications
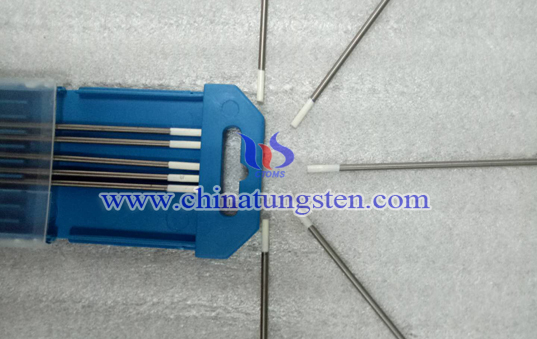
Zirconiated tungsten electrodes are used in TIG/GTAW welding and in plasma arc welding.It has to be bought with care. There are many companies which manufacture tungsten electrodes. Among all the pure metals, tungsten has the highest melting temperature. A tungsten electrode that is of high quality will arc easily, have an improved arc time and result in a good quality weld with minimum contamination. The tungsten electrode should have very small grain structure and allowing for better migration of oxides to the tip. You can have clean finish or ground finish tungsten electrodes. Clean finish tungsten electrodes are the ones that have been chemically cleaned. Ground finish tungsten electrodes are the ones that have been ground to a uniform shape with a polished surface. This makes them right for optimal heat conduction. The tungsten electrodes should meet the ISO6848 and AWS A5.12 standards.
There has been a lot of improvement in the manufacture of tungsten electrodes. The addition of oxides to pure tungsten has resulted in tungsten alloys that give the same level of emission as pure alloys but at a much lower temperature. This helps in improving the arc time of the electrode and the arc stability.
It is best to choose a tungsten electrode that performs well with all metals and all welding power sources for hand held welding. For all types of automated welding operations, it is best to choose the type of tungsten electrode that suits it, through testing it.
Each oxide has a different physical characteristic. This affects the work of the tungsten electrodes. This is color coded and shows us with which oxide it is mixed. There is no standard for these color codes and can vary in U.S., Europe and Japan.
After choosing the blend of oxide with tungsten to suit your needs, you should choose the diameter of the tungsten electrode. They are available in packages of ten in a variety of standard diameters. Choosing the diameter of the tungsten electrode is important as it will affect the welding performance and welding bead shape.
In welding with tungsten, an arc of electricity is created between the tungsten electrode and the material to be welded. A filler metal is fed into the molten metal pool while welding. This process requires an air or water cooled torch to keep the tungsten electrode in place as it is connected to the TIG welder. The welding equipment should adhere to the norms set by the government and have GTAW in quality standards.
Different types of tungsten electrodes are used for different purposes. Pure tungsten electrodes are used for general use and are classified as WP or EWP. Cerium oxide and lanthanum oxide help in improving arc stability. They also help in starting easily and decreases burn-off. Thorium oxide is especially designed for DC operations. It can also handle high temperatures. Since it is radioactive and inhalation of the fumes while grinding thorium can be hazardous to health. Thorium electrodes can be replaced with greater concentration of lanthanum electrodes. Zirconiated electrodes increase current capacity, increases electrode life, improves arc stability and starting. Manufacturers can also manufacture other tungsten alloys that will be with specific metal additions which will follow EWG classification under the AWS system.